In logistics and e-commerce, two essential terms often come into play: “pick and pack” and “fulfillment.” These processes are pivotal in getting products from the shelves to your customers’ doorsteps. In this blog, we’ll break down what “pick and pack” and “fulfillment” mean, explore their pros and cons, and help you decide which best suits your business.
What is Pick and Pack?
Pick and pack is the core process within a warehouse or fulfillment center. It’s all about selecting the right items from inventory and carefully packaging them for customer shipment. Picture this: you’ve ordered a pair of sneakers online, and in a pick and pack facility, a worker picks those sneakers from the storage area and packs them securely in a box, ready for shipping.
What is Fulfillment?
On the other hand, fulfillment encompasses a broader set of services that go beyond pick and pack. It includes everything from order processing to warehousing, inventory management, shipping, and often customer support. Think of it as the whole package – your one-stop solution for everything related to order fulfillment.
The Pros of Pick and Pack
Now that we’ve got the basics down, let’s dive into the pros and cons, starting with pick and pack.
1. Precision and Control: You have precise control over each step in the pick and pack process. This means you can customize procedures, ensuring that each customer order receives meticulous attention.
2. Flexibility: Need to adapt quickly to changes in demand? Pick and pack allows for swift procedure adjustments, making it ideal for businesses facing seasonal fluctuations.
3. Cost Efficiency: Efficient pick and pack operations can reduce labor and shipping expenses, helping your business save money.
4. Inventory Management: Regular picking helps you keep tabs on your inventory levels, preventing stockouts and overstock situations and ensuring you always have the right products.
5. Quality Control: You can implement quality checks during picking to minimize errors, ensuring that your customers receive top-notch products.
The Cons of Pick and Pack
While pick and pack has its merits, it’s not without its downsides:
1. Labor Costs: Managing an in-house pick and pack operation often involves hiring and overseeing warehouse staff, which can be expensive.
2. Infrastructure Costs: Setting up your warehouse, buying equipment, and implementing technology requires a significant upfront investment.
3. Seasonal Variability: If your business faces seasonal demand, it can take time to scale up or down quickly enough to meet fluctuations in orders.
4. Complexity: Managing pick and pack processes, especially in more extensive operations, can be complex and require specialized software and systems.
5. Limited Resources: Smaller businesses or startups might need more resources or expertise to efficiently handle in-house fulfillment, which can lead to inefficiencies and errors.
6. Risk of Errors: Even with precise procedures, there’s always a risk of errors during the pick and pack process, leading to shipping mistakes and customer dissatisfaction.
7. Competitive Disadvantage: Competitors who opt for third-party fulfillment might have cost advantages and more scalable operations.
The Pros of Fulfillment
Now, let’s explore the advantages of fulfillment:
1. Outsourced Expertise: Fulfillment providers are experts in their field, offering comprehensive services to help you focus on your core business activities.
2. Scalability: Fulfillment services are highly scalable, making them an excellent choice as your business grows.
3. Cost Savings: By outsourcing to fulfillment centers, you can save on warehousing and labor costs and benefit from shipping discounts due to their volume.
4. Multichannel Sales: If you sell products through various channels, fulfillment providers can manage the complexity of handling diverse order streams efficiently.
5. Time Savings: Outsourcing your fulfillment processes frees up your time, allowing you to concentrate on strategic aspects of your business, like marketing and product development.
The Cons of Fulfillment
However, fulfillment isn’t without its drawbacks:
1. Less Control: While you gain convenience, you relinquish some control over the pick and pack process to the third-party fulfillment provider.
2. Communication Challenges: Coordinating with an external provider can sometimes lead to communication challenges, potentially affecting order accuracy or customer support.
3. Dependency: Relying on a third party for critical aspects of your business leaves you dependent on their performance, which can be a concern if they encounter issues or delays.
4. Costs: Although outsourcing can save money in some areas, fulfillment services come with their fees, which may affect your overall cost structure.
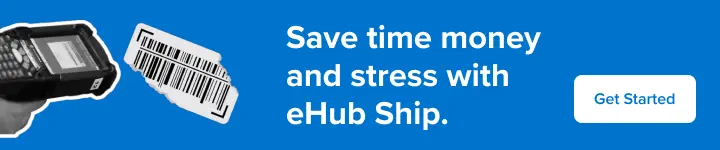
How to Decide: Pick and Pack vs. Fulfillment
Now that we’ve weighed the pros and cons, let’s discuss how to make an informed decision between pick and pack and fulfillment:
1. Evaluate Your Business Needs: Begin by assessing the specific needs of your business. Consider your order volume, the nature of your products, and your budget.
2. Forecast Growth: Think about your business’s growth trajectory. If you anticipate rapid growth, a scalable fulfillment solution may be the way to go.
3. Analyze Costs: Compare the costs of in-house pick and pack versus outsourcing to a fulfillment provider —factor in immediate expenses and long-term implications.
4. Consider Control vs. Convenience: Determine how much control you want over the order fulfillment process. If you prioritize control, in-house pick and pack may be preferable. If convenience is a priority, consider outsourcing.
5. Assess Your Expertise: Consider your team’s expertise in fulfillment processes. If you lack experience in logistics, outsourcing to experts may be the wiser choice.
6. Analyze Customer Expectations: Keep your customers in mind. If they demand fast, accurate deliveries, prioritize a solution that meets those expectations.
7. Seek Recommendations: Talk to other businesses in your industry and seek recommendations. Their experiences can provide valuable insights.
8. Test the Waters: If unsure, you can always test both approaches. Start with in-house pick and pack, and assess whether outsourcing makes sense as your business grows.
Conclusion
In conclusion, both pick and pack and fulfillment have merits and downsides. The choice ultimately hinges on your business’s unique needs, goals, and resources. By carefully evaluating your situation and considering the factors outlined here, you can make an informed decision that sets your business on the path to successful order fulfillment.