Introduction
In e-commerce, meeting customer expectations is non-negotiable. One of the critical factors in achieving this is efficient warehousing fulfillment. This engine powers your e-commerce operation, ensuring that orders are processed accurately, products are stored securely, and deliveries reach customers promptly.
In this comprehensive guide, we’ll delve into the world of warehousing fulfillment, exploring its components, highlighting its importance, and providing strategies to help you master this essential aspect of e-commerce.
What Is Warehousing Fulfillment?
Before we dive into strategies and tips, let’s start with the basics. What exactly is warehousing fulfillment?
Warehousing fulfillment, also known as order fulfillment, encompasses a range of activities within the supply chain. It begins when a customer orders and ends when it is successfully delivered. This process includes order processing, inventory management, picking, packing, shipping, and handling returns.
The Importance of Efficient Warehousing Fulfillment
Now that we understand warehousing fulfillment let’s explore why it’s so crucial in e-commerce.
1. Customer Satisfaction: Efficient fulfillment ensures customers receive their orders accurately and on time, leading to higher satisfaction rates.
2. Repeat Business: Happy customers are likelier to become repeat customers. Smooth order fulfillment contributes to customer loyalty.
3. Brand Reputation: Timely and accurate deliveries contribute to a positive brand image, while fulfillment mishaps can tarnish it.
Critical Components of Warehousing Fulfillment
Effective warehousing fulfillment involves several core components:
1. Order Processing: This is the first step in the fulfillment process. Orders are received, verified, and entered into the system for processing.
2. Inventory Management: Managing inventory is critical. It involves keeping track of stock levels, restocking products as needed, and ensuring that products are organized.
3. Picking: Warehouse staff locates the necessary items from the inventory after receiving an order. The efficiency of this process is crucial for timely fulfillment.
4. Packing: The picked items are packed securely and appropriately for shipping. Proper packaging ensures that products arrive in good condition.
5. Shipping: Once packed, the orders are dispatched for delivery to the customer. Choosing a suitable shipping carrier and method is part of this process.
6. Returns Handling: Besides outbound shipments, efficient fulfillment includes processing customer returns. This involves inspecting returned items, restocking them if possible, and managing refunds or exchanges.
Technology Integration in Warehousing Fulfillment
Technology plays a pivotal role in modern warehousing fulfillment. Here’s how technology is integrated into the process:
1. Route Optimization: Advanced routing software helps determine the most efficient and cost-effective routes for transporting goods, minimizing fuel consumption and transit times.
2. Tracking and Monitoring: Real-time tracking systems allow you to monitor the progress of your shipments, providing valuable insights into delivery times and potential delays.
3. Inventory Management: Inventory management systems track stored goods precisely, ensuring you always have the right products when needed.
Tips for Efficient Warehousing Fulfillment
Now that we’ve covered the key components let’s dive into some actionable tips for achieving efficient warehousing fulfillment:
1. Optimize Inventory: Regularly review your inventory and identify slow-moving items. Consider discounting or promoting them to clear space and improve cash flow.
2. Streamline Order Processing: Automate as much as possible to reduce human errors and speed up the fulfillment process.
3. Implement Efficient Picking Strategies: Implement picking strategies that best suit your business, whether batch picking, zone picking, or wave picking.
4. Invest in Packaging: Use quality packaging materials to protect products during shipping. Consider eco-friendly options to align with sustainability trends.
5. Choose the Right Shipping Partners: Evaluate and select shipping carriers based on cost, reliability, and delivery speed. Negotiate favorable shipping rates whenever possible.
The Role of Scalability in Warehousing Fulfillment
Scalability is a critical consideration in warehousing fulfillment. As your business grows or experiences fluctuations in demand, you need a fulfillment process that can adapt. Here’s how scalability plays a role:
1. Seasonal Fluctuations: Many e-commerce businesses experience seasonal peaks in demand. Scalable fulfillment allows you to handle higher order volumes during these periods efficiently.
2. Business Growth: As your business expands, you’ll need a fulfillment process to grow with you. Scalability is critical for adding new product lines or entering new markets.
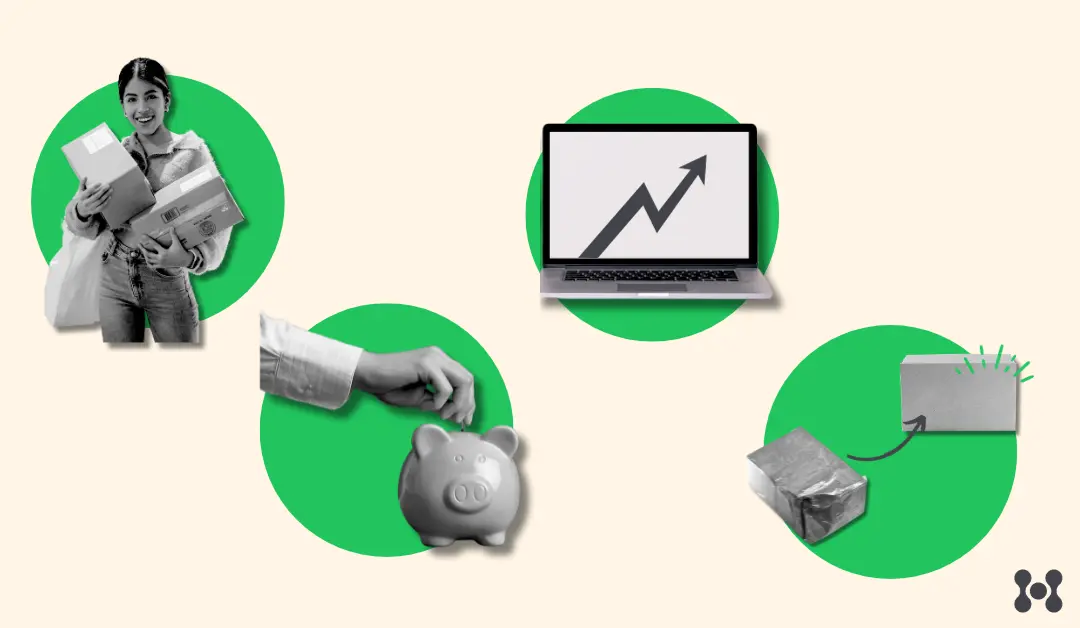
Outsourcing Warehousing Fulfillment
For many e-commerce businesses, managing warehousing fulfillment in-house can be challenging. This is where outsourcing comes into play, and third-party logistics (3PL) providers can be invaluable partners.
1. Expertise: 3PL providers are specialists in warehousing fulfillment. They have the expertise and experience to manage the process efficiently.
2. Cost-Effectiveness: Outsourcing can often be more cost-effective than maintaining your warehousing and fulfillment operations. You avoid the costs of warehouse space, staff, and technology investments.
3. Focus on Core Activities: By outsourcing, you can focus on core business activities like marketing, product development, and customer service while leaving the complexities of fulfillment to experts.
Challenges and Solutions in Warehousing Fulfillment
Efficient fulfillment has its challenges. Here are some common hurdles and solutions:
→ Challenge 1: Coordination Complexity. Coordinating transportation and warehousing activities can be complex, especially for businesses with extensive operations.
→ Solution: 3PL providers excel in coordination, streamlining processes, and optimizing routes.
Challenge 2: Technology Integration. Integrating advanced technology solutions can be daunting for some businesses.
→ Solution: 3PL providers often have extensive experience implementing and managing technology, making integration smoother.
Choosing the Right 3PL Provider
If you decide to outsource warehousing fulfillment, here are factors to consider when selecting the right 3PL partner:
1. Industry Expertise: Look for providers with experience in your specific industry or niche, as they’ll understand your unique logistics needs.
2. Service Offerings: Ensure the provider offers the services you require, whether specialized transportation, temperature-controlled storage, or other specific needs.
3. Geographic Coverage: Consider whether the provider’s geographic coverage aligns with your distribution areas or expansion plans.
Conclusion
In the world of e-commerce, efficient warehousing fulfillment is the key to customer satisfaction, repeat business, and brand reputation. By understanding its components, integrating technology, and implementing best practices, you can master the art of warehousing fulfillment.
Whether you manage it in-house or partner with a 3PL provider, optimizing your fulfillment process will ultimately contribute to the success and growth of your e-commerce business.