Introduction
Buying or renting a warehouse is a massive step for any entrepreneur or e-commerce business. Needing a more significant place to house all your sellable goods is an excellent problem. Many e-commerce businesses opt to purchase the warehousing space and fulfill and pack the orders in-house.
In recent years, a whole new branch of e-commerce has developed where warehousing, picking, and shipping has become a business entity in and of itself. To stay competitive, many e-commerce businesses look at outsourcing their warehouse management to a third party called a Distribution Processing Center or DPC. This blog post will dive into what a distribution processing center is. We will also discuss what services they offer and the pros and cons of deciding to outsource this part of your business.
Main Points:
- Distribution Centers are a marriage between warehouses and fulfillment centers.
- Distribution Processing Centers house, fulfill, and ship orders for businesses.
- Pros include efficiency and support for business growth.
- Cons include less oversight over this process and opening your business to other industry risks.
Distribution Processing Center Defined
A Distribution Processing Center is the marriage between a warehouse and a fulfillment center. DPC’s house and store products like a warehouse. They also pick, pack, and ship these products like a fulfillment center. In this way, Distribution Processing Centers combine the best of both worlds. They offer a one-stop shop for all your fulfillment and distribution needs. Their value proposition is DPC’s offer of dialed-in logistics and data-driven processes. That makes this portion of commerce as fast and efficient as possible. Their business is ensuring products are housed safely and shipped quickly.
What Services Do Distribution Processing Centers Provide?
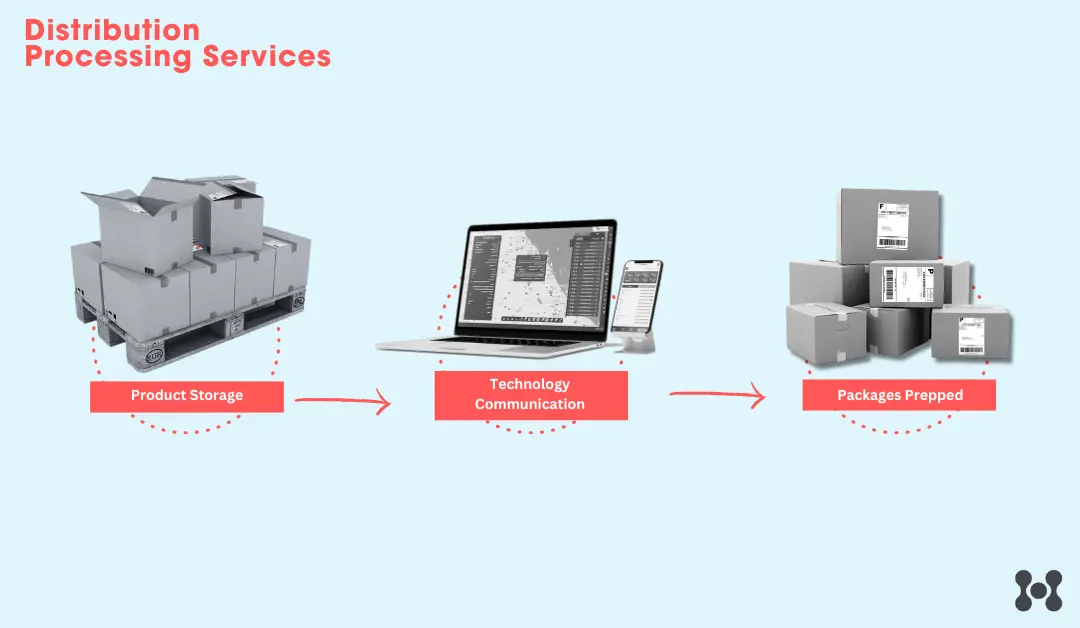
- First, DPC’s offer storage of your products. Warehouses hold products for long periods of time. DPC’s will house your product but require a fast turnover rate. DPCs will accept the products on your company’s behalf and organize and store the products efficiently. This prepares your product to be packaged when an order is placed.
- Once an order is placed, technology is used to communicate between your selling platform and the Distribution Processing Center. The order will then be fulfilled in an accurate and timely manner.
- Lastly, once the item has been prepped for shipping, a label will be purchased. Then, the label will be put on the outside of the package and handed off to a third-party carrier for delivery.
Main Pros of Distribution Processing Centers
Cost: Because these centers are shipping in high volumes, they can get quantity discounts on shipping rates that may not be available to a business. Businesses often find it an even split when they go to a processing center. Even though they are paying a higher fee per unit to pick and package an item, the savings in shipping make it a break-even situation. Another place you can save as a business owner is by hiring your own staff to pick and ship products. Outsourcing this part of your business means you can rely on the highly trained staff of DPC’s instead of hiring your own staff to complete this process.
Supporting business Growth: Your business can reach a certain point where to keep up with demand, it makes sense to outsource to a Distribution Processing Center. This choice can bolster your business and stabilize the fulfillment and shipping process. This, in turn, has a positive impact on your customers.
Shipping Speed: This is a distribution center’s bread and butter. Shipping items correctly and quickly is a top priority. Both businesses and customers can learn to count on this reliability. A DPC’s primary goal is to expedite the movement of goods.
Automation: DPC’s strategic use of technology gives them the upper hand in many cases. Automated systems, such as conveyor belts, robotic arms, and RFID technology, actively contribute to an uninterrupted product flow. These systems boost productivity, reduce human errors, and accelerate order fulfillment.
Additional Pros of Distribution Processing Centers
Enhanced inventory management: Distribution Processing Centers can monitor stock levels in real-time and communicate stock levels to businesses by using cutting-edge technology. This helps prevent stockouts and educates businesses on the demand for their products. Businesses can then use that information to empower them to repurchase inventory and appropriate times. Using data to make these decisions instead of their best guesses will improve the bottom line overall.
Environmentally Conscious: DPCs actively participate in eco-friendly initiatives by optimizing transport routes, using energy-efficient machinery, and embracing sustainable packaging solutions. This environmentally conscious approach resonates with customers who value businesses’ commitment to sustainability and ultimately work to reduce their carbon footprint.
Handling Seasonal Demands: Seasonal fluctuations can strain supply chains immensely, especially during peak holiday periods. DPCs actively prepare for these surges by scaling up their operations, strategically allocating resources, and collaborating with suppliers and logistics partners.
Cons of Distribution Processing Centers:
Quality Control: Anytime you outsource a part of your business, miscommunications will happen. These miscommunications can lead to errors and hurt your business’s reputation. There are steps that both distribution processing centers and companies can take to mitigate these risks. Anytime you bring in an outside business, there is a higher risk of this happening.
Industry Disruptions: Distribution Processing Centers will also be subject to industry disruptions such as labor strikes and adverse weather. Additionally, they can be subject to delivery equipment disruptions, such as breakdowns and repairs and economic depressions or recessions. All of them can negatively impact operations.
At eHub, we understand the challenge e-commerce companies face when choosing to work with a Distribution Processing Center. eHub has worked tirelessly to find quality, well-vetted DPCs that fit individualized company needs. If you need to outsource fulfillment and shipping but are intimidated by the process, reach out to eHub today, and we will work to find an ideal solution for your business.
Conclusion
In conclusion, Distribution Processing Centers offer a marriage of warehousing and fulfillment centers. By constantly implementing new technologies, DPCs have made inventory management, order fulfillment, and shipping into a well-oiled art form.