Introduction
Warehouses play a vital role in the global supply chain. They are crucial in enabling the smooth flow of goods from one point to another. The world is becoming more automated. Thus, a warehouse control system ensures maximum operational efficiency and accuracy.
In this blog, we will explain WCSs, discuss their pros and cons, and explain how to choose the right one for your business.
What is a Warehouse Control System?
A Warehouse Control System (WCS) is software that manages and optimizes warehouse operations, including inventory management, order picking, and shipping. WCSs work alongside Warehouse Management Systems (WMS) to provide real-time control and visibility into warehouse operations.
WCSs are responsible for managing individual tasks within the warehouse, such as directing automated equipment, picking and putaway operations, and shipping and receiving. Thus, by integrating with WMSs, WCSs help optimize warehouse processes, reducing waste, increasing efficiency, and improving accuracy.
Pros and Cons of WCSs
Like any technology, WCSs have their pros and cons. Therefore, here are some benefits and drawbacks to consider when choosing a WCS for your warehouse.
Pros
1. Increased Efficiency
Firstly, WCSs can automate many tasks traditionally performed by human workers. This reduces the risk of human error and increases the speed and efficiency of warehouse operations.
2. Improved Accuracy
WCSs also leverage real-time data and analytics. They can help reduce errors and improve accuracy in warehouse operations, which in turn leads to fewer mistakes and improved customer satisfaction.
3. Reduced Labor Costs
Further, WCSs automate many of the tasks traditionally performed by human workers. Thus, WCSs can help reduce labor costs and improve profitability.
4. Scalability
Finally, WCSs can be scaled up or down depending on the size and needs of your warehouse. This makes it easier to adapt to changing business needs.
Cons
1. High Initial Investment
First, implementing a WCS can be expensive, requiring significant capital expenditures upfront.
2. Training and Maintenance
Additionally, as with any technology, training and maintenance requirements can be a large burden on warehouse staff.
3. Risk of Downtime
Next, there is a risk of “downtime”. Any technology system is vulnerable to downtime. Moreover, this leads to lost productivity and revenue.
4. Limited Flexibility
Finally, some WCSs may have limited flexibility. Thus, they require significant customization to adapt to specific business needs.
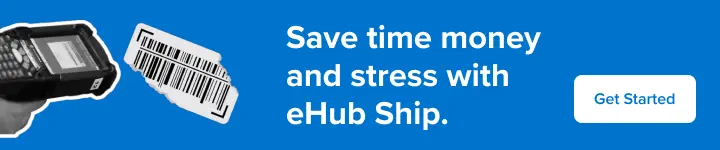
How to Choose the Right WCS
Choosing the right WCS for your warehouse is crucial. It can make or break efficiency and productivity. Here are some factors to consider when selecting a WCS.
1. Compatibility
First, ensure that your WCS is compatible with your warehouse management system. Also, check its compatibility with other systems you may have in place.
2. Scalability
Next, let’s talk about scalability. Choose a WCS that can be scaled up or down depending on the size and needs of your warehouse.
3. Integration
Look for a WCS that can integrate with other systems. For instance, check integration with transportation management systems. Why? Because this helps provide end-to-end visibility into your supply chain.
4. Customization
Additionally, consider a WCS that can be customized to meet your specific business needs.
5. Support and Maintenance
Ensure that the WCS you choose comes with robust support and maintenance options. This helps to minimize downtime and disruptions.
How to Implement a WCS
Implementing a WCS requires careful planning and execution to ensure a smooth transition from the current system to the new one. Here are some steps to follow when implementing a WCS.
1. Assess Your Current System
First, conduct a thorough analysis of your current warehouse system to identify areas for improvement.
2. Define Your Objectives
Second, clearly define your goals for implementing a WCS.
3. Choose the Right System
Third, choose a WCS that meets your specific business needs and requirements.
4. Plan Your Implementation
Fourth, develop a detailed plan for implementing the WCS. Further, the plan should include timelines, budgets, and resources.
5. Train Your Staff
Provide complete training to your staff to ensure they are comfortable using the new system.
6. Monitor and Evaluate
Continuously monitor and evaluate the new system’s performance to find areas for revision. Then, make those critical changes.
Conclusion
In summation, WCSs are vital in ensuring maximum efficiency in warehouse operations. By automating many tasks traditionally performed by human workers, WCSs can help reduce labor costs, improve accuracy, and increase efficiency. When selecting a WCS, it’s vital to consider several factors. For example, this can include compatibility, scalability, integration, customization, and support and maintenance. Further, this helps ensure you choose the right system for your business needs. Therefore, with planning and execution, implementing a WCS can help take your warehouse operations to the next level.